Vacuum meters, often referred to as vacuum gauges or vacuum pressure gauges, are essential instruments used to measure pressure in vacuum systems. These devices play a critical role in various industrial applications, scientific research, and even everyday tasks, ensuring that processes operate efficiently and safely. This article will delve into the types of vacuum meters, their working principles, applications, and the importance of accurate vacuum measurement.
Types of Vacuum Meters
Vacuum meters can be classified into several categories based on their working principles. The most common types include:
- Mechanical Vacuum Gauges: These gauges operate based on mechanical principles. They include Bourdon tube gauges and diaphragm gauges. Bourdon tube gauges consist of a curved tube that straightens under pressure, moving a pointer on a dial to indicate pressure levels. Diaphragm gauges use a flexible diaphragm that deforms under pressure changes, providing a mechanical displacement that is translated into a pressure reading.
- Electronic Vacuum Gauges: These gauges employ electronic sensors to measure pressure. They include capacitance manometers and piezoelectric sensors. Capacitance manometers measure the change in capacitance due to the movement of a diaphragm in response to pressure changes. Piezoelectric sensors convert mechanical stress into an electrical signal, providing accurate readings of vacuum levels.
- Thermal Vacuum Gauges: Thermal gauges, such as thermocouple gauges and thermal conductivity gauges, measure vacuum by assessing the heat transfer characteristics of gases. Thermocouple gauges measure temperature changes caused by gas conduction, while thermal conductivity gauges measure the ability of gas to conduct heat away from a heated element.
- Ionization Vacuum Gauges: These are high-vacuum gauges that measure pressure based on the ionization of gas molecules. They work by generating ions in a gas sample and measuring the resulting current. Ionization gauges are particularly useful in ultra-high vacuum applications, such as in semiconductor manufacturing and scientific research.
Working Principles
The working principle of vacuum meters varies depending on their type. Mechanical gauges rely on physical displacement mechanisms, while electronic and thermal gauges utilize electronic signals or thermal properties of gases. Regardless of the method, all vacuum meters provide a means to convert pressure into a readable format, allowing operators to monitor and control vacuum conditions effectively.
Applications of Vacuum Meters
Vacuum meters are widely used across various industries and applications. Some common uses include:
- Manufacturing and Processing: In industries like food processing, pharmaceuticals, and chemical manufacturing, maintaining a specific vacuum level is crucial for quality control, product preservation, and process efficiency.
- Laboratories and Research: Scientific research often requires precise vacuum conditions for experiments, such as in physics and materials science. Vacuum meters ensure that researchers can maintain the necessary environmental conditions for their studies.
- Semiconductor Industry: In semiconductor fabrication, ultra-high vacuum environments are essential for processes like deposition and etching. Vacuum meters are critical for monitoring and controlling these conditions to ensure product quality and yield.
- Pumps and Systems Testing: Vacuum meters are used to test the performance of vacuum pumps and systems, ensuring they are operating within desired specifications.
Importance of Accurate Measurement
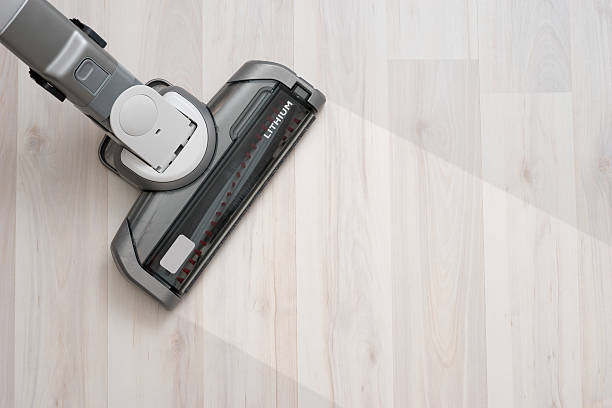
Accurate measurement of vacuum levels is crucial for several reasons:
- Safety: In industries where hazardous materials are handled, accurate vacuum measurement ensures that processes operate safely, minimizing the risk of leaks and exposure.
- Quality Control: In manufacturing, precise vacuum levels can significantly impact product quality. Inadequate vacuum conditions can lead to defects, reduced shelf life, and increased waste.
- Operational Efficiency: Monitoring vacuum levels helps optimize processes, reducing energy consumption and operational costs.
Conclusion
Vacuum meters are indispensable tools in various industries, providing critical measurements that ensure safety, quality, and efficiency. With advancements in technology, these instruments have become more accurate and reliable, enabling industries to meet the increasing demands of modern manufacturing and research. Understanding the different types of vacuum meters, their working principles, and their applications is essential for anyone involved in vacuum-related processes, as it contributes to better management and control of vacuum systems. As industries continue to evolve, the role of vacuum meters will only become more significant, highlighting their importance in the future of technology and manufacturing.